Advanced SNCR/SCR Denitrification Solutions
SNCR offers a cost-effective approach for moderate NOx reduction, while SCR provides higher efficiency, achieving up to 90% reduction. Both solutions enhance overall environmental performance, helping companies reduce their carbon footprint and promote sustainable operations.
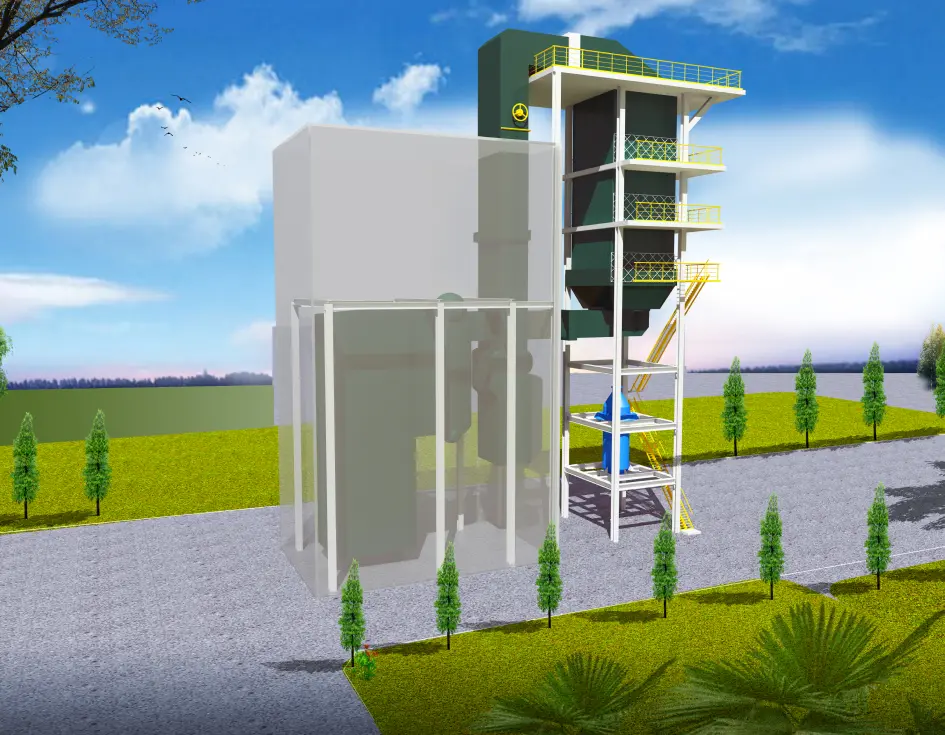
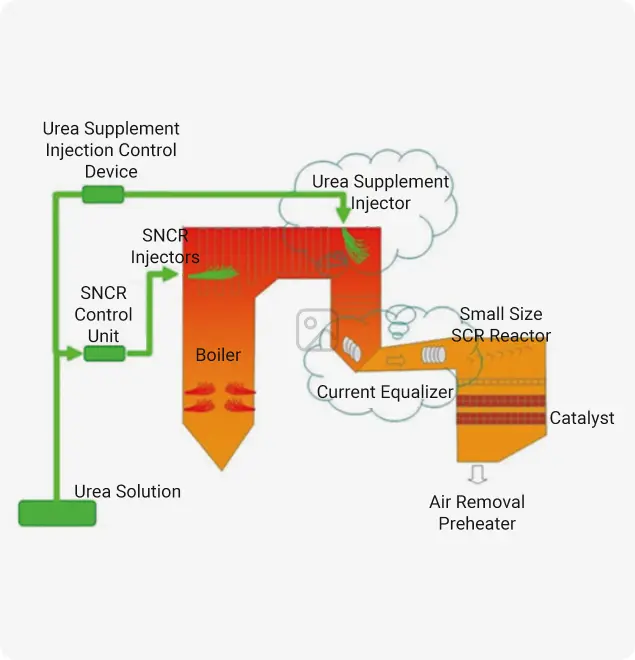
Cost-Effective NOx Reduction for Industrial Applications
High-Efficiency NOx Reduction for Demanding Industrial Needs
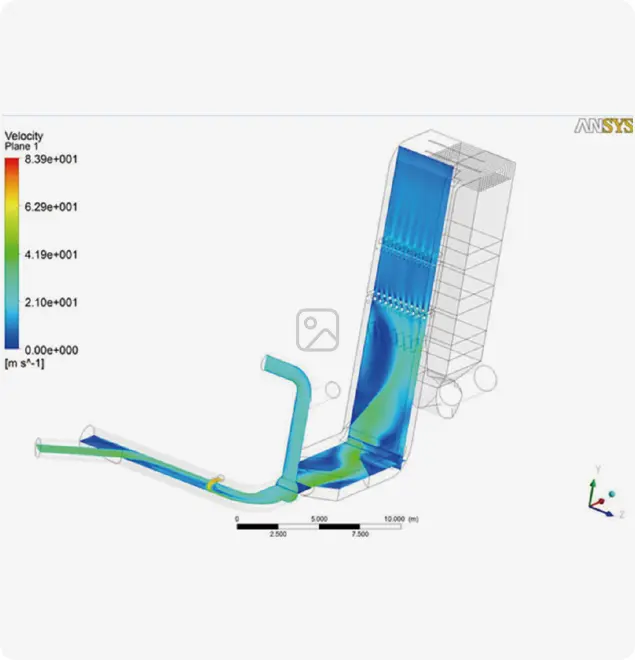
SNCR vs SCR
Criteria | SNCR | SCR |
---|---|---|
Cost | Lower initial cost | Higher initial cost |
Efficiency | Moderate NOxreduction(30-50%) | High NOx reduction (up to 90%) Up to 90% |
Reduction Rate | 30-50% NOx reduction | Up to 90% NOx reduction |
Operating Temperature | 850-1100°C | 300-400°C |
Catalyst Required | No | Yes |
Typical Applications | Industrial boilers, waste incineration, cement kilns | Power plants, refineries, large industrial boilers |
Maintenance Requirements | Lower maintenance, simpler system | Higher maintenance, more complex system |
Want to Know More About Technical Specifications of SNCR/SCR Denitrification Solutions?
Proven Solutions in Real-World Scenarios
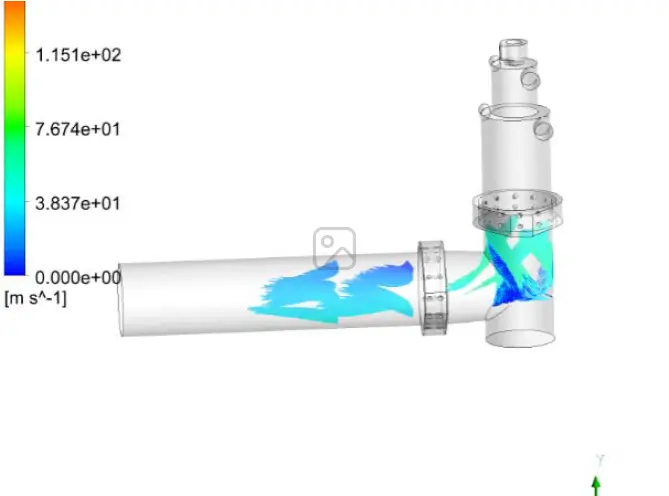
Reducing NOx Emissions

Energy Efficiency and Environmental Sustainability

Customized Solutions
Leading Comprehensive Solutions for Industrial
Pollution Control
We specialize in providing industry-leading air pollution control technologies and solutions, helping businesses effectively manage industrial emissions and comply with global environmental standards.
Ready to Reduce NOx Emissions with Advanced Solutions?
Our Most Frequently Asked Questions
SCR (Selective Catalytic Reduction) uses a catalyst to achieve up to 90% NOx reduction, while SNCR (Selective Non-Catalytic Reduction) operates without a catalyst, achieving 30-50% reduction. SCR is more effective but has higher costs.
SCR reduces NOx by injecting ammonia into flue gas in the presence of a catalyst, converting NOx into nitrogen and water. SNCR injects urea or ammonia into high-temperature flue gas, reacting without a catalyst to lower emissions.
SCR systems offer high-efficiency NOx reduction (up to 90%), making them suitable for power plants and large industrial boilers. They ensure compliance with strict air pollution control regulations.
Choose SNCR if you need a cost-effective solution for moderate NOx reduction, especially in industrial boilers, waste incineration, or cement kilns. It is ideal for projects with limited budgets and less stringent emission standards.
Power generation, refineries, waste-to-energy plants, and chemical plants benefit greatly from SCR, where achieving high levels of NOx reduction is essential for meeting environmental regulations.
Yes, SNCR is often used in smaller industrial boilers and incinerators due to its lower initial costs and simpler design, making it ideal for businesses seeking moderate emission control solutions.
SCR systems are generally more expensive than SNCR due to the catalyst requirement and complex installation. Costs vary depending on the size and scope of the project but are justified by their high efficiency in NOx reduction.
SCR systems require regular maintenance of the catalyst to ensure efficiency, while SNCR systems are simpler, with lower maintenance needs. Maintenance for both is essential to maintain optimal air pollution control.
Yes, a combined SNCR/SCR system can provide a balance between cost and efficiency. This approach is useful in cases where high NOx reduction is needed but cost considerations are also important.
Both technologies help industries comply with NOx emission limits set by environmental agencies. By reducing nitrogen oxides, they help businesses avoid penalties and contribute to cleaner air quality standards.
More Comprehensive Solutions for Industrial Pollution Control
We specialize in providing industry-leading air pollution control technologies and solutions, helping businesses effectively manage industrial emissions and comply with global environmental standards.
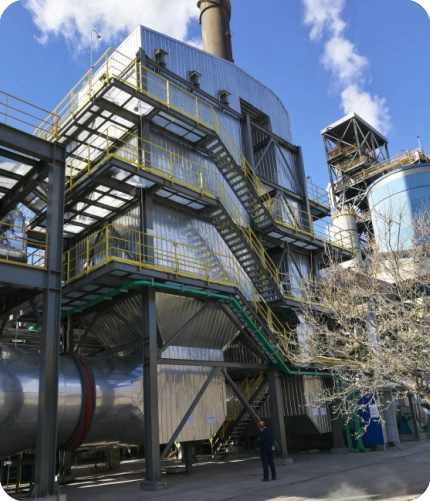
SNCR/SCR denitrification technology
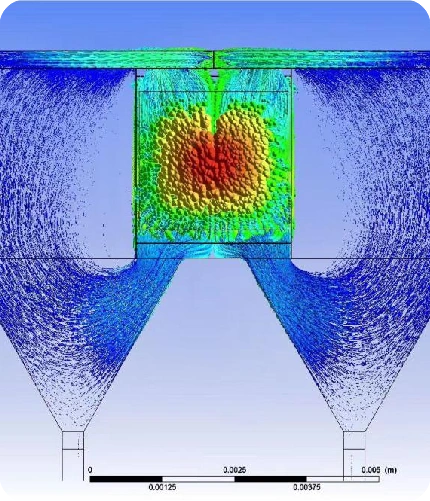
NOx pol-lutant control optimization
SNCR denitrification lance arrangement optimization
CFB semi-dry fluidized bed simulation
Urea pyrolysis analysis simulation
CFD Flow Field Simulation
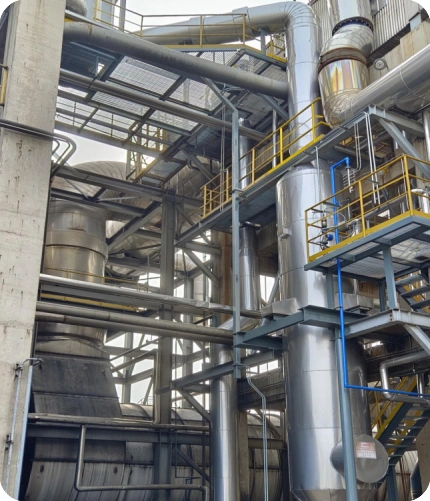
Urea pyrolysis furnace equipment
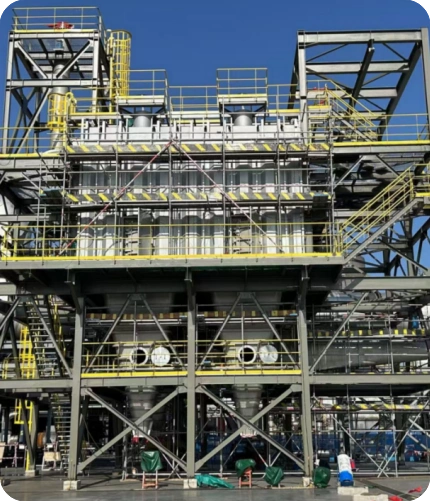
Bag filter
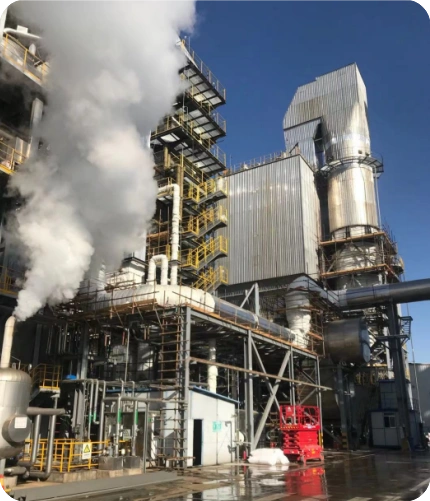
Flue Gas Desulfurization
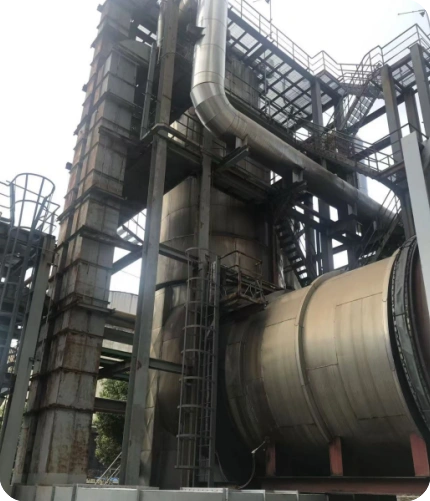